Цифровой двойник от Росатома: революция в атомном машиностроении
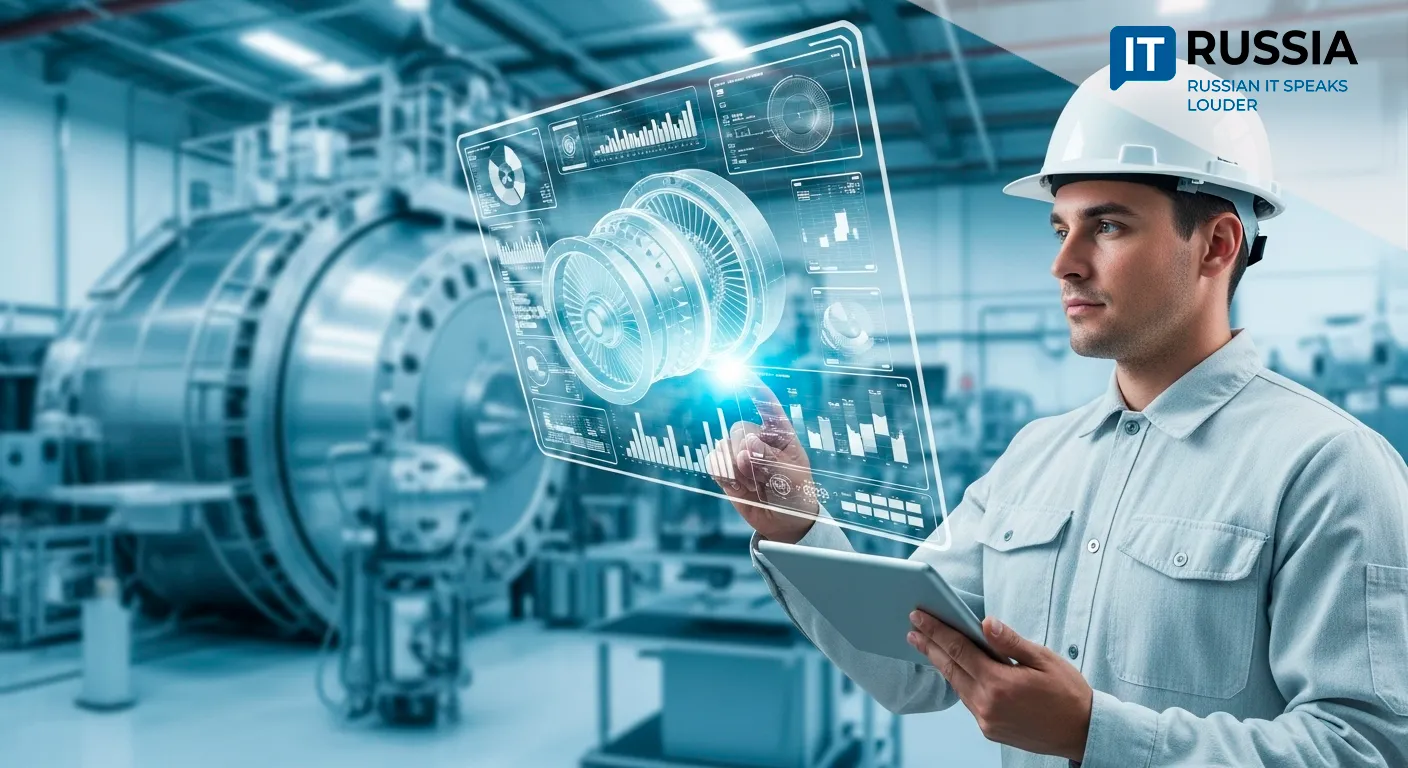
Росатом внедрил технологию, отслеживающую состояние изделий на всех этапах — от проектирования до обслуживания, сокращая время поиска информации в 3–4 раза. Это позволяет автоматизировать до 30% операций по сбору данных.
В реальном времени отслеживать состояние продукции
В 2025 году АО «АЭМ», машиностроительный дивизион госкорпорации «Росатом», успешно внедрило систему «Цифровой двойник изделия» на базе low-code платформы «Атомкод», созданной ЧУ «Цифрум». Система позволяет в реальном времени отслеживать состояние продукции — от проектирования до передачи заказчику и последующего обслуживания. Она охватывает ключевые процессы, включая контроль качества, логистику и техническое обслуживание, обеспечивая прозрачность и точность данных. Внедрение сократило время поиска информации в 3–4 раза, с часов до минут, и уменьшило ручные операции на 30%, минимизируя ошибки и затраты. Например, проверка данных о сложных компонентах, таких как насосы для АЭС, теперь занимает менее 15 минут вместо часа.
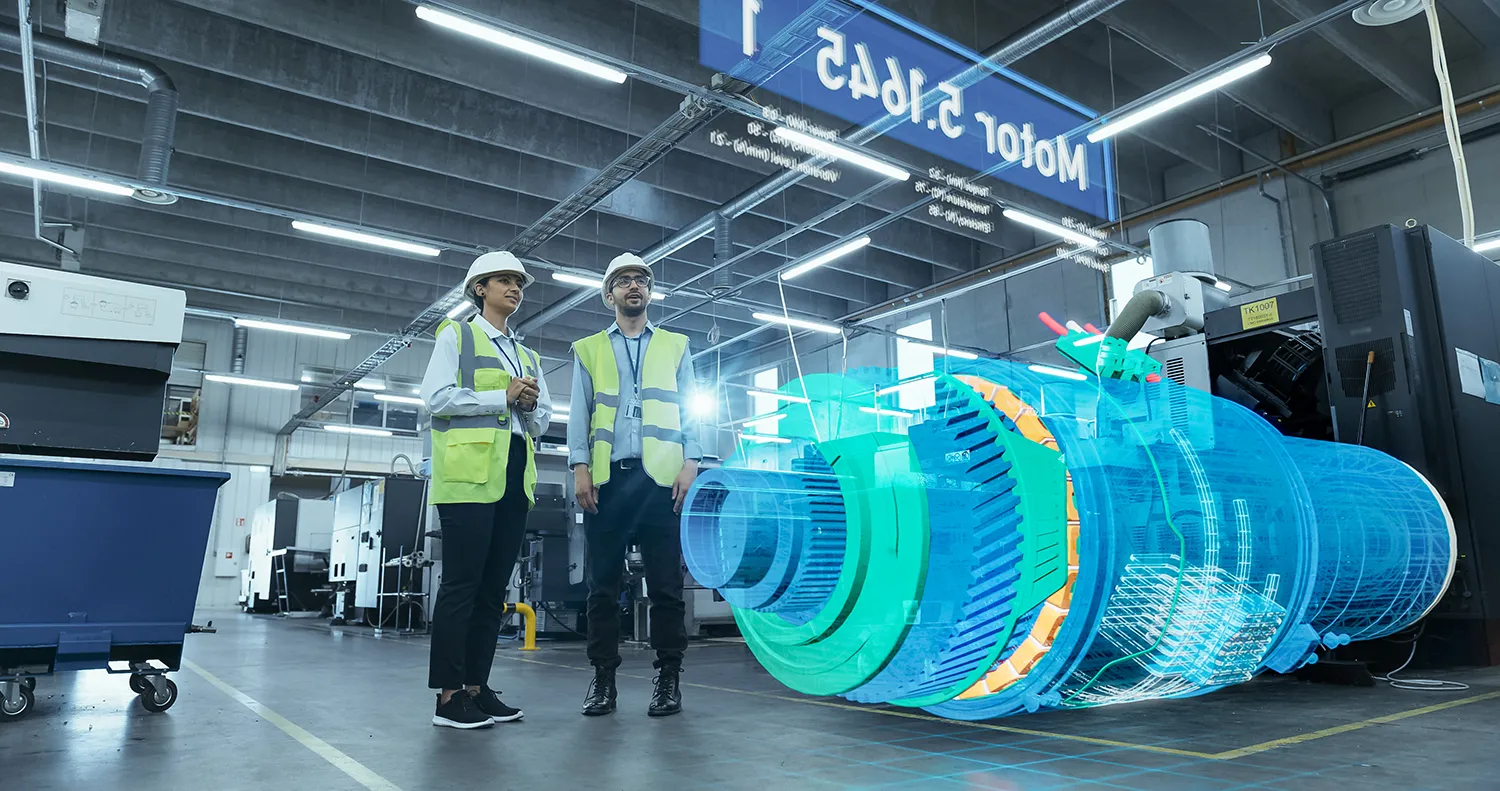
Разработка системы заняла всего два месяца, что в разы быстрее традиционных сроков в 4–6 месяцев для кастомизированных решений. Это стало возможным благодаря гибкости low-code платформы «Атомкод», которая позволяет быстро адаптировать функционал под задачи без глубокого программирования. Это укрепляет технологический суверенитет России, снижая зависимость от иностранного ПО, такого как SAP или Oracle. Для мировой аудитории проект демонстрирует способность России создавать конкурентоспособные IT-решения для наукоёмких отраслей, таких как атомное машиностроение, где точность и надёжность критически важны.
Перспективы развития
Система «Цифровой двойник изделия» обладает высоким экспортным потенциалом. Платформа «Атомкод» может быть адаптирована для управления проектами в странах, где Росатом реализует строительство АЭС, таких как Египет («Эль-Дабаа»), Индия («Куданкулам») и Турция («Аккую»). Эти страны нуждаются в эффективных инструментах для цифровизации сложных процессов, и low-code решения, такие как «Атомкод», предлагают доступную альтернативу западным платформам.
Cистема масштабируется на другие дивизионы Росатома, включая производство топлива и ядерных реакторов, а также на машиностроительные предприятия, такие как Уралмаш. Low-code формат позволяет быстро адаптировать её под разные изделия — от турбин до медицинского оборудования. Например, интеграция с ИИ расширит функционал, позволяя предсказывать износ и оптимизировать логистику.
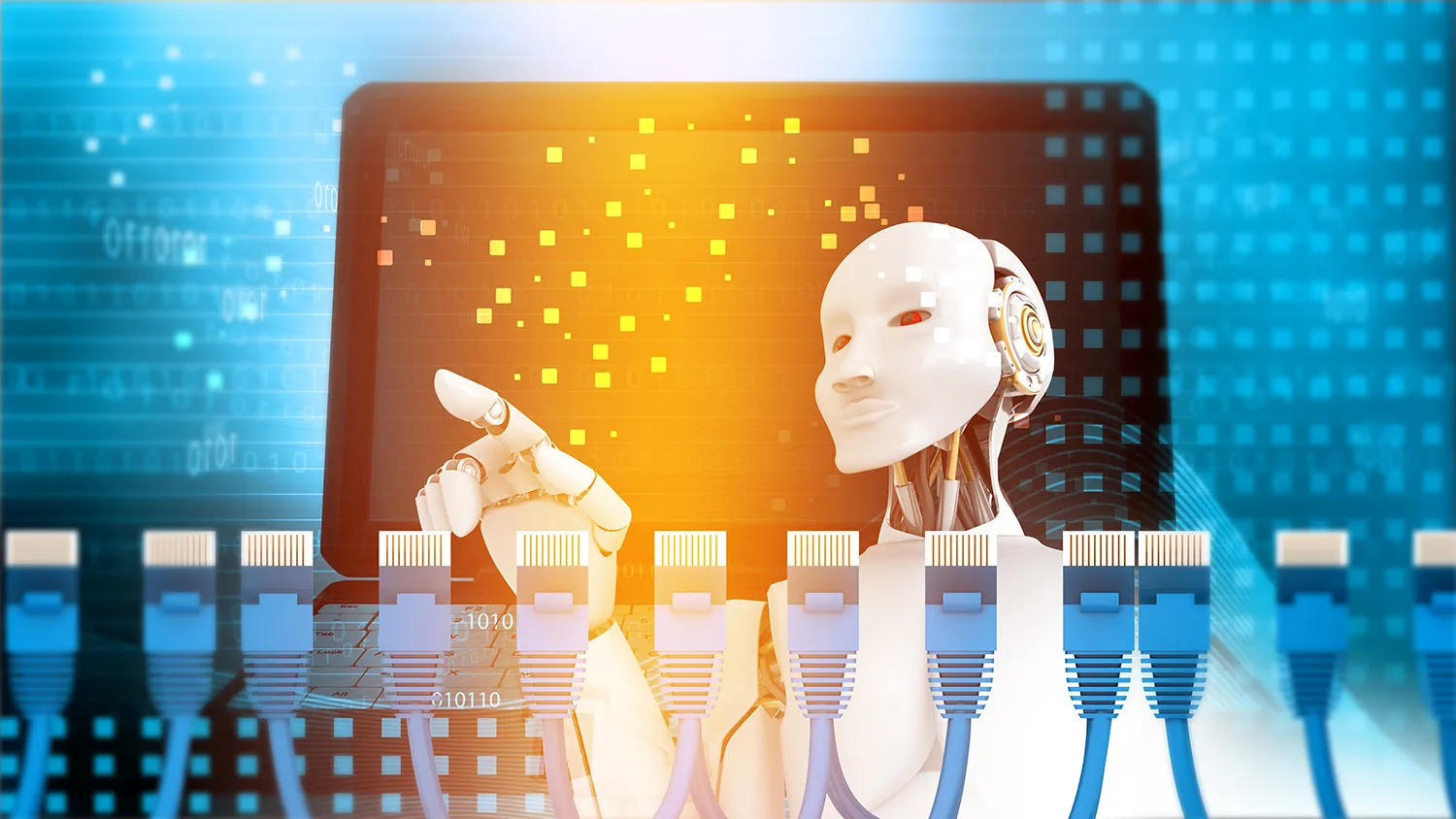
Цифровые двойники нужны всем
За последние пять лет интерес к цифровым двойникам в России значительно вырос. В 2022–2023 годах Уралвагонзавод и КБ «Титан» тестировали цифровые двойники для оборонной продукции, но на кастомных решениях, требующих длительной разработки. В 2023 году спрос на отечественные low-code платформы увеличился, с первыми кейсами в энергетике (МРСК) и угольной отрасли (партнёрство с СБИС).
В 2024 году госпрограмма «Цифровая индустрия» стимулировала внедрение цифровых двойников в металлургии, например, на ЧТПЗ и Северстали, но на базе ERP/SCADA-систем. В 2025 году предприятия оборонного и энергетического секторов перешли на отечественное ПО, однако low-code решения, такие как «Атомкод», остаются новаторскими. Платформы, такие как OutSystems и Mendix, набирают популярность в промышленности по всему миру, но российские разработки выделяются интеграцией с ядерными технологиями.
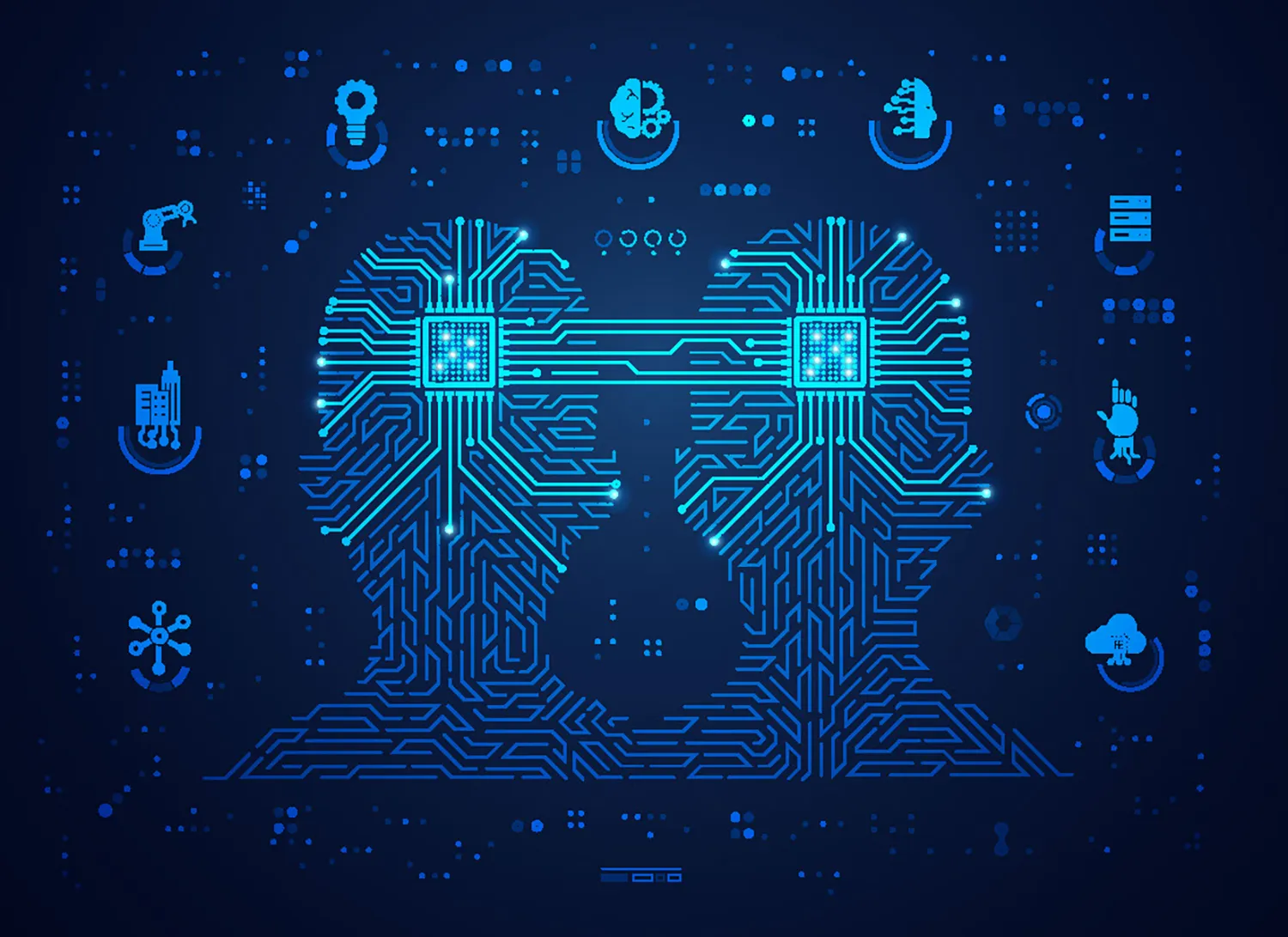
Сокращает затраты и ускоряет процессы
Система «Цифровой двойник изделия» демонстрирует эффективность low-code платформ в атомной отрасли. Она сокращает затраты, повышает надёжность и ускоряет процессы, укрепляя позиции России в цифровизации промышленности.
К 2026 году ожидается масштабирование технологии на другие предприятия Росатома и машиностроения, а также экспорт в страны СНГ и БРИКС. Это усилит технологический суверенитет и создаст новые возможности для международного сотрудничества.