Underground Edge: How Russia Is Reinventing Mine Logistics With On-Site Intelligence
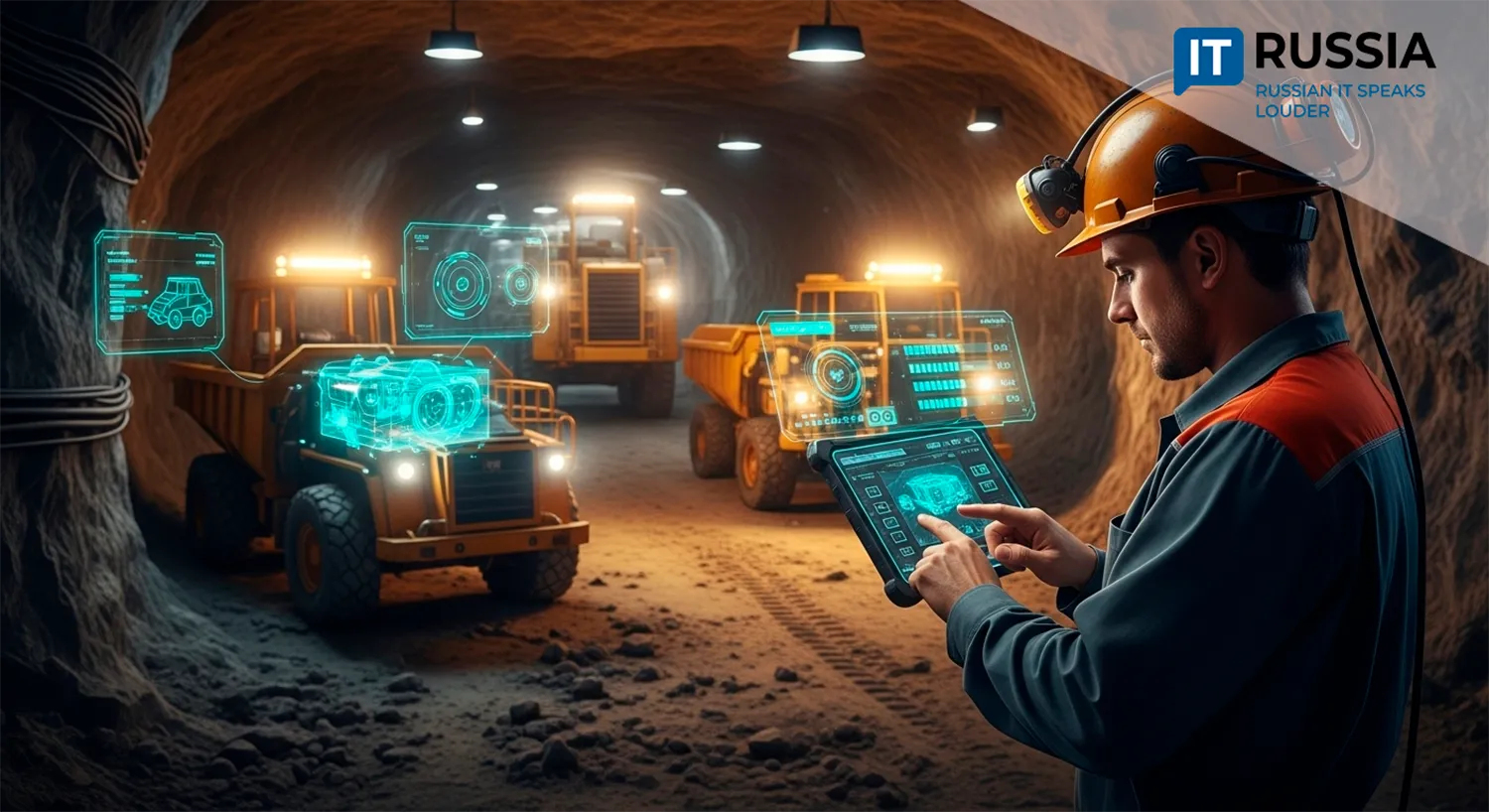
EuroChem’s latest deployment of edge-based monitoring at a potash mine marks a milestone in digitizing industrial logistics where cloud access isn’t viable.
Real-Time Intelligence Without the Cloud
Implementing edge technology in mining is no small feat, particularly in environments with complex infrastructure and high operational loads. At its Usolskiy Potash Plant in Russia’s Perm Territory, EuroChem has launched the country’s first real-world edge-monitoring system for underground transportation.
The breakthrough lies in how data is processed: directly on-site, without relying on cloud centers. This drastically reduces network strain, increases system responsiveness, and enhances failure detection in real time. In environments like deep mines, where signal instability and delayed reaction times can compromise safety and uptime, edge architectures are emerging as the optimal solution.
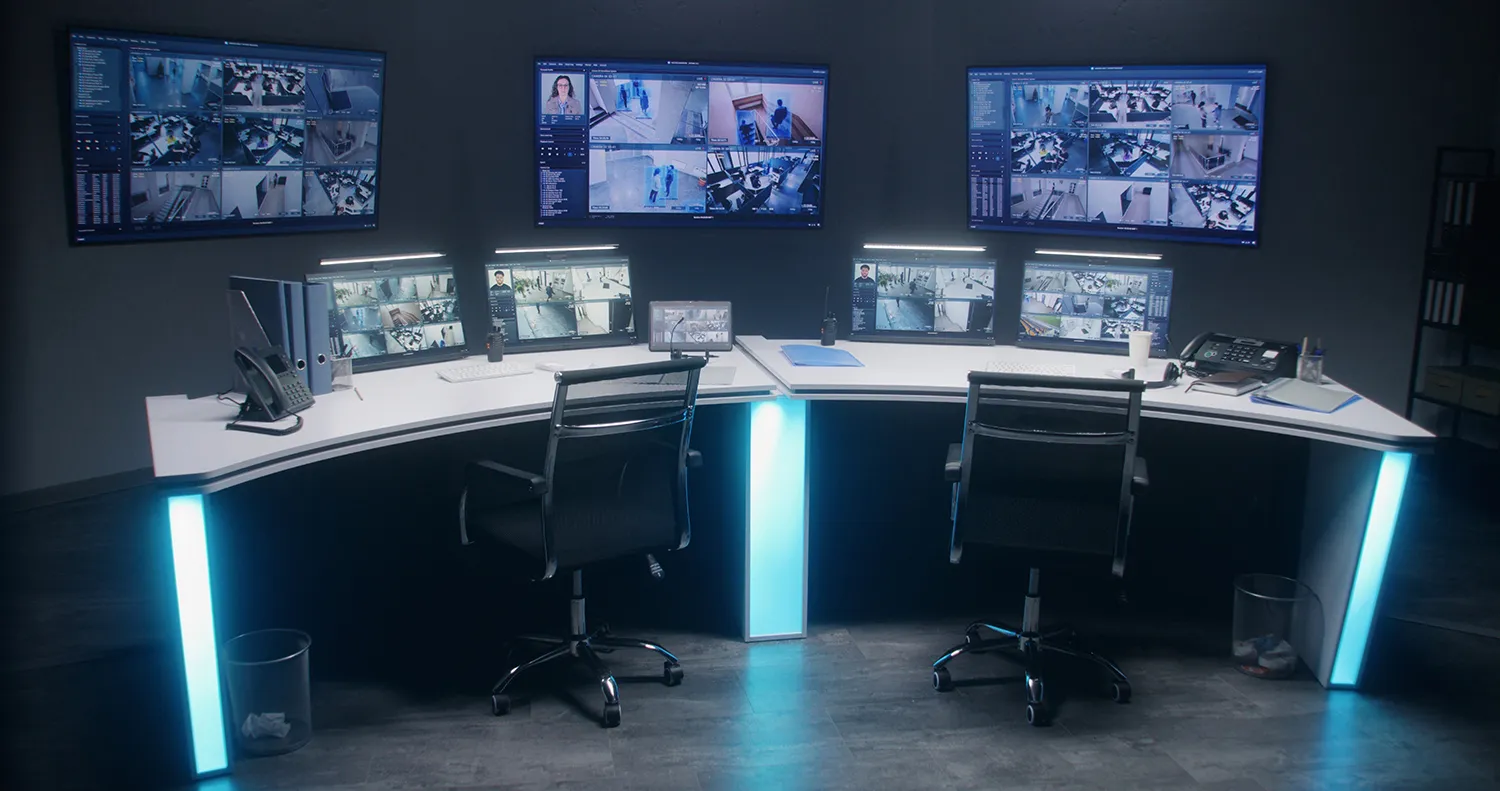
The project is significant on multiple fronts: it showcases Russia’s ability to produce world-class digital systems, improves transparency and safety in resource extraction, and supports national efforts toward technological sovereignty in critical infrastructure.
From Subterranean Trials to Surface Logistics
While the system was built for underground use, it’s highly adaptable. EuroChem plans to scale it to surface logistics hubs and processing facilities like VolgaKaliy starting in 2025. Edge systems are especially valuable in industries with unstable connectivity and tight uptime requirements—making them a fit for global markets in regions like South America and Southeast Asia.
Designed to operate under extreme conditions—dust, humidity, thermal stress—this edge system bypasses cloud licenses and provides localized, Russian-language interfaces. Its resilience makes it competitive with Western alternatives, particularly for developing economies with infrastructure constraints.
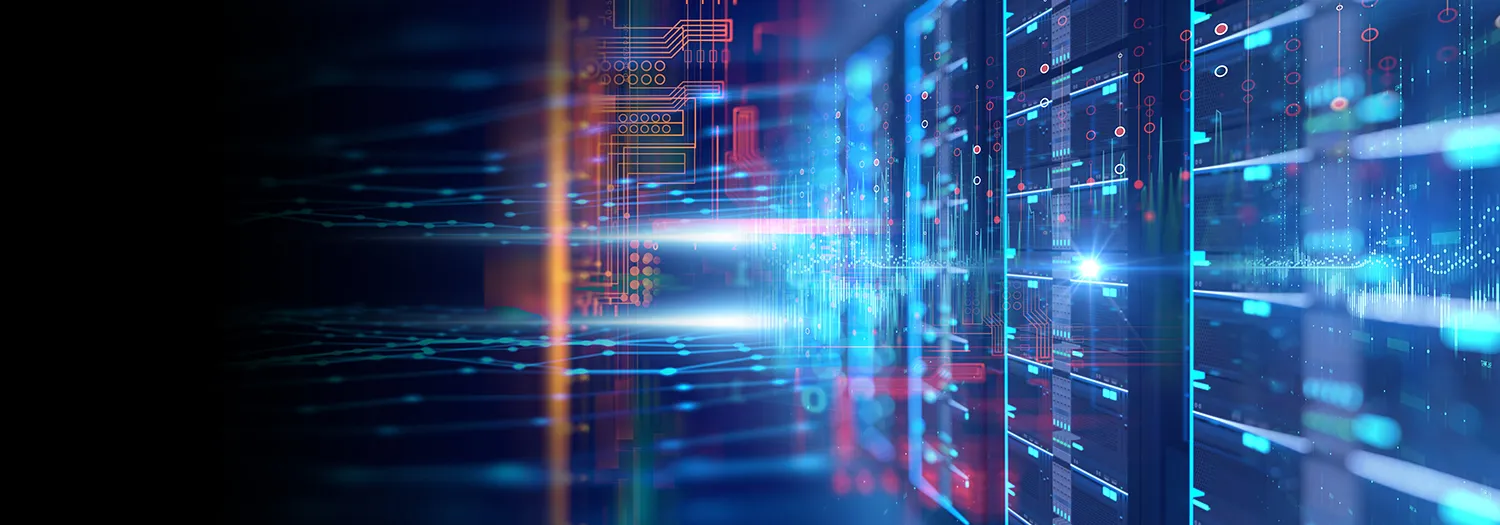
Five Years of Edge Evolution
Russia’s edge journey didn’t begin overnight. Between 2022 and 2023, steel plants adopted predictive maintenance with local servers. In 2023–2024, Rosneft brought edge computing to its drilling platforms. In 2024, Norilsk Nickel deployed AI modules in mines, powered by localized processors to assess underground risks. Rail terminals also began using locally hosted dispatch systems, forming the foundation for a logistics-wide digital transformation.
All of these initiatives share one trait: data is processed locally, shielding operations from geopolitical risks and external disruptions. EuroChem’s project is a continuation of this larger trend—edge architecture as a new reliability standard.
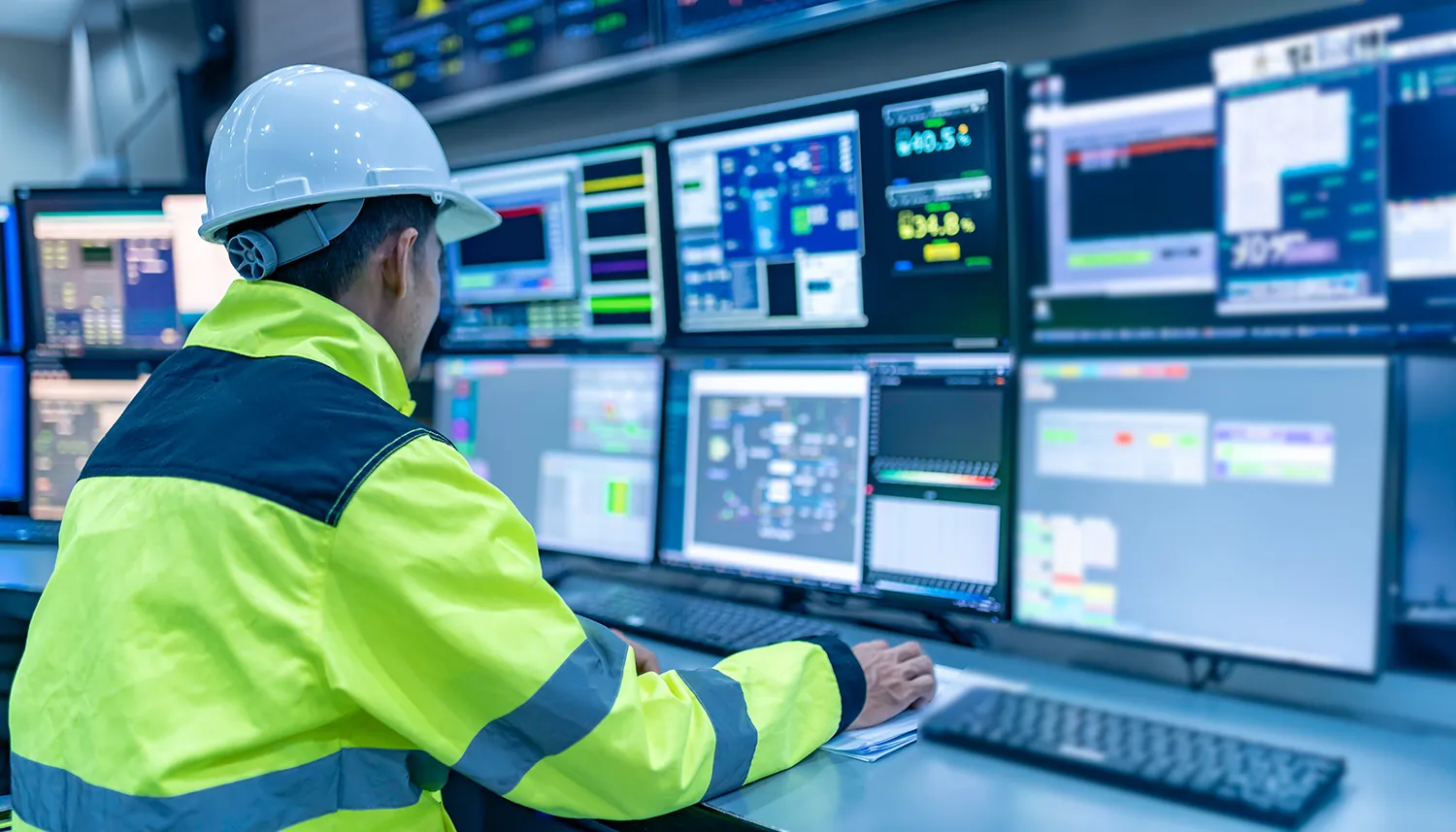
Smart Algorithms in Mining Uniform
The Usolskiy deployment is more than a tech story—it’s a signal that heavy industry digitalization is not only possible, but already underway. And it’s happening without spectacle, under challenging conditions, with precise engineering.
In the next 2–3 years, localized edge monitoring will likely become standard in Russian industry, spawning a range of domestic solutions built for real-world workloads. International rollout will target extraction-intensive economies with extreme operating environments.
Over 3–5 years, these systems will be integrated into broader digital ecosystems—from underground transport to surface logistics and process automation. Their convergence with intelligent transport control (ITSU TP) frameworks could redefine efficiency and safety at scale.