AI-Driven Aluminum: RUSAL Unveils Vision System for Smelter Process Optimization
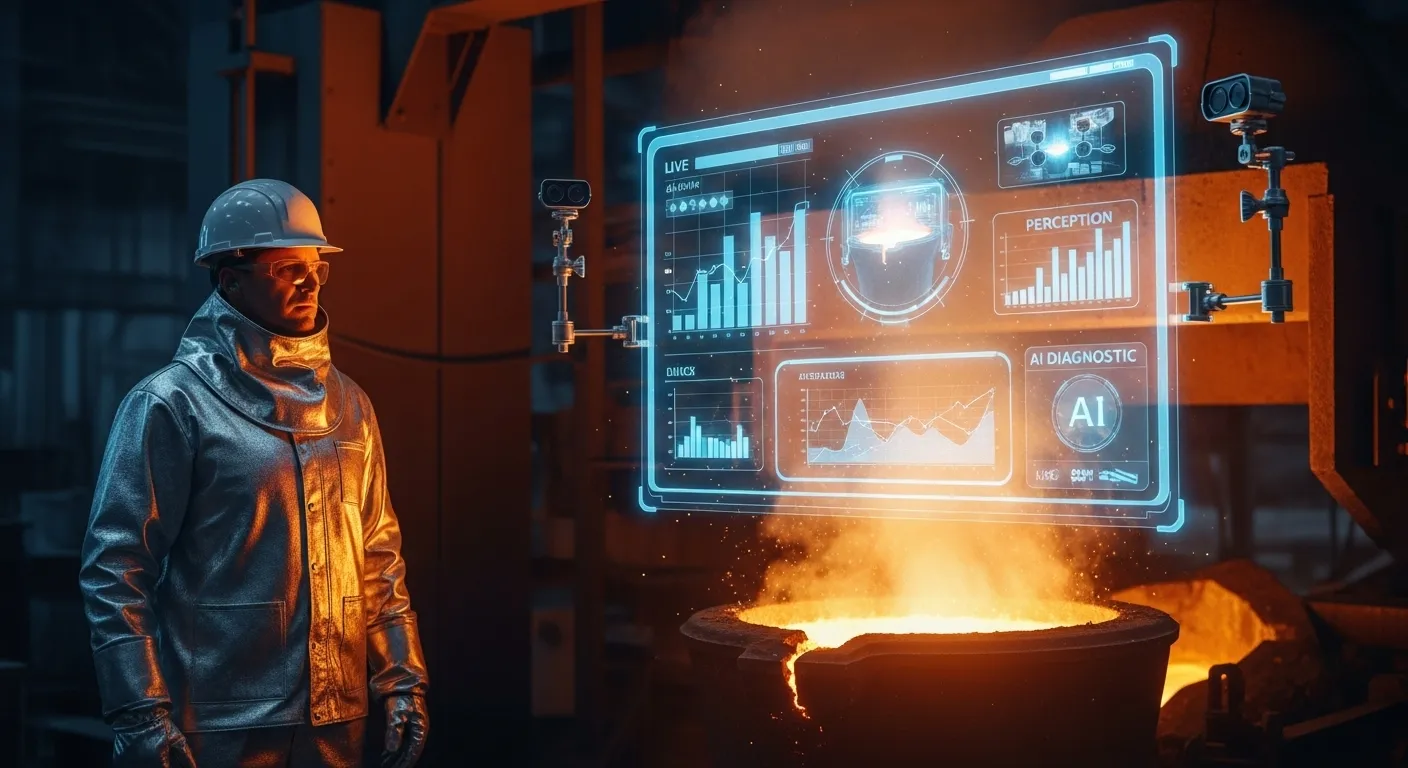
Russia’s industrial digitalization has entered a new phase, where artificial intelligence systems are not just analyzing operations but actively perceiving and responding to real-time changes in production environments. Metallurgical giant RUSAL has unveiled its industrial AI platform, pushing aluminum manufacturing into a new era of precision and autonomy.
From Analytics to Perception: Industrial AI Evolves
RUSAL’s new system represents a shift in how AI integrates with manufacturing—from passive analytics to active perception. On aluminum casting lines, the process involves 7 to 20 sequential operations depending on the alloy and type of ingot. Each step must be executed precisely and in strict accordance with technical specifications.
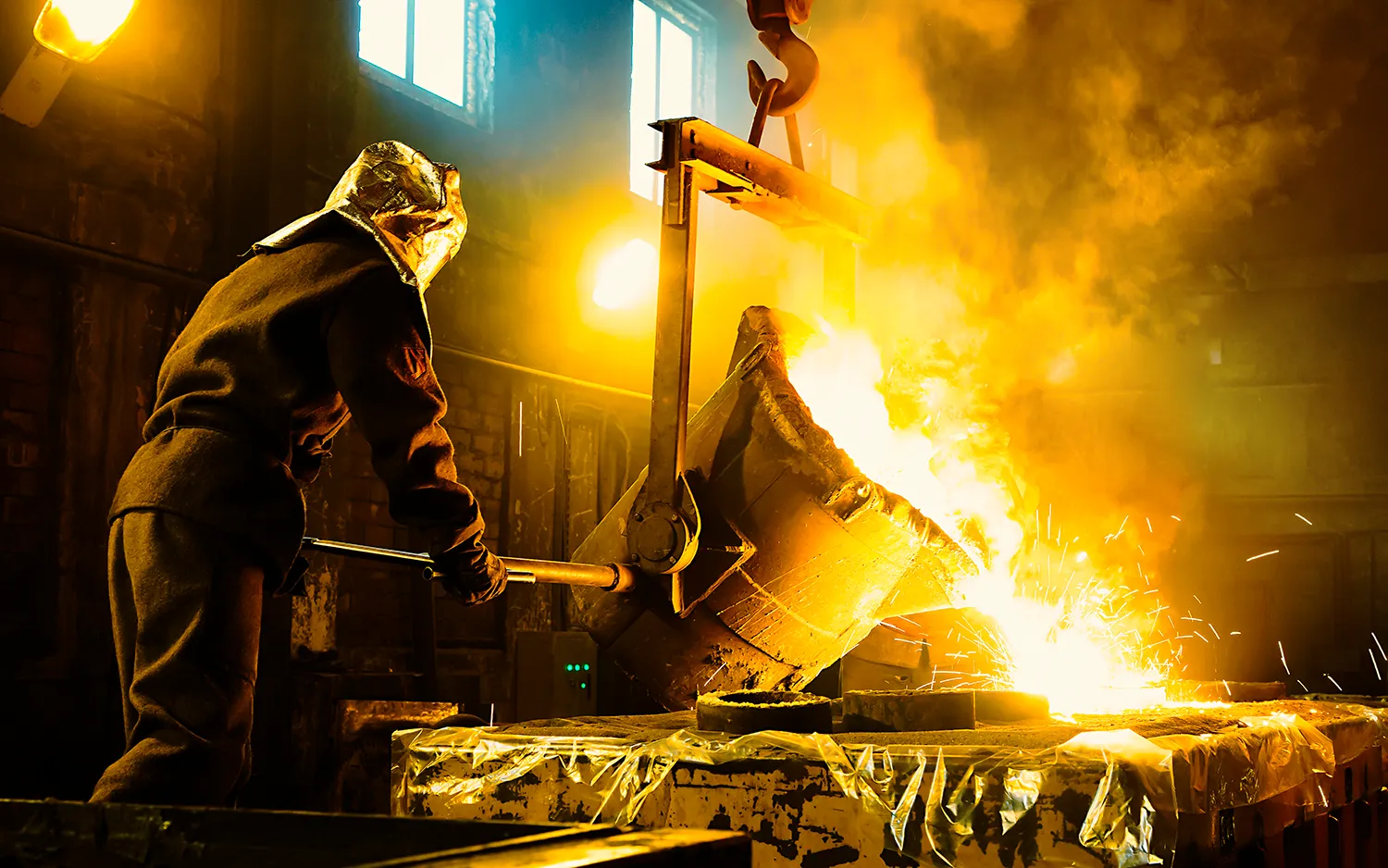
RUSAL’s innovation involves real-time camera monitoring of molten metal parameters, with AI algorithms instantly flagging any deviation. This gives AI ‘perception’—the ability to interpret physical cues in the production environment, transforming the role of AI from observer to participant.
Quality, Efficiency, and Worker Safety
One of the most immediate benefits of RUSAL’s system is the drastic reduction in substandard products. With AI regulating every step, output quality has become predictably consistent. The continuous nature of metallurgical processes also makes automation critical—minimizing human presence on the shop floor boosts both efficiency and safety.
RUSAL’s platform optimizes raw material and energy consumption, trimming production costs while ensuring operational continuity. Fewer personnel on-site means less exposure to industrial hazards. The competitive advantage comes from a combination of improved quality and cost savings throughout the value chain.
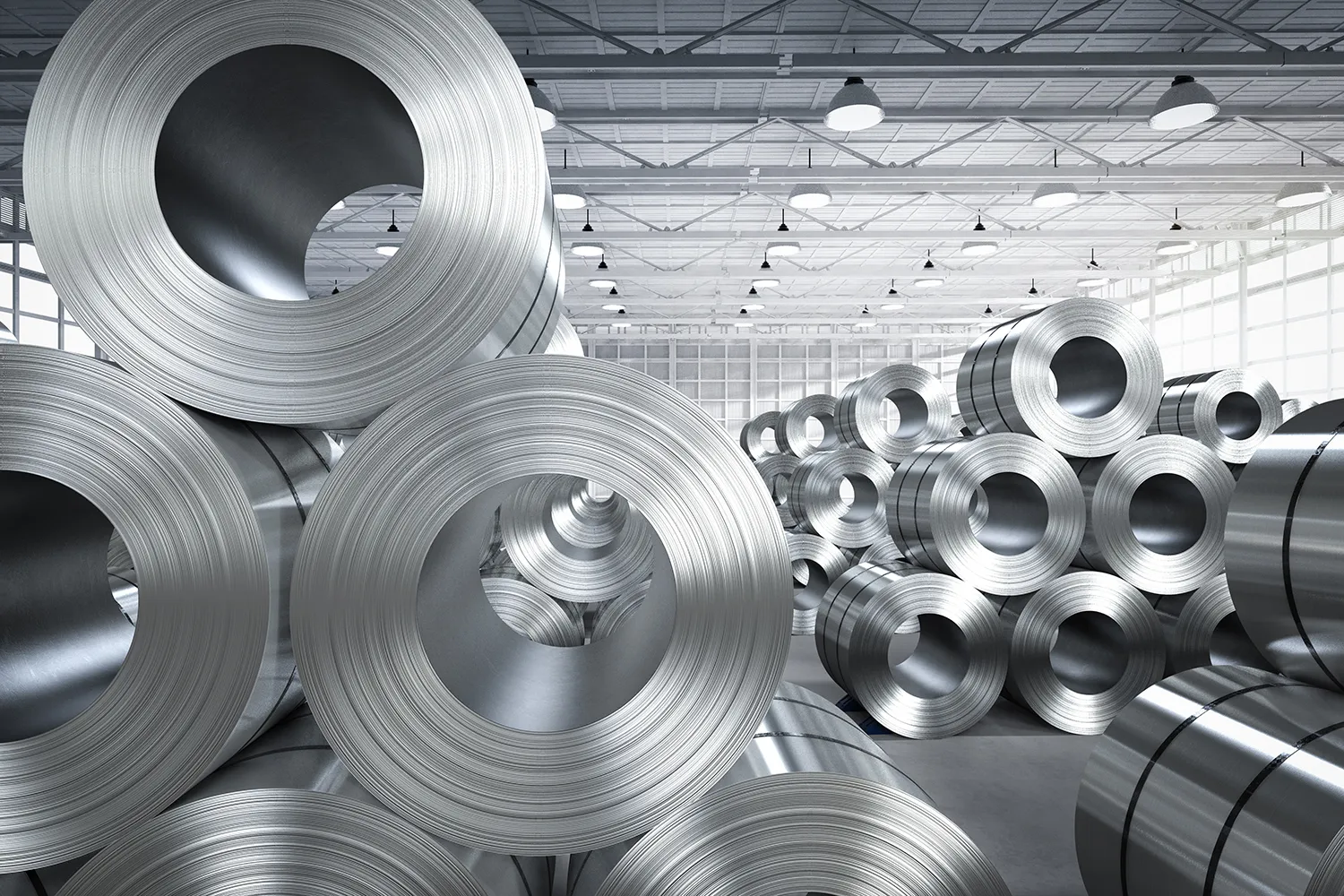
Homegrown Tech with Scalable Impact
What makes the project even more notable is that it was developed internally by RUSAL’s own Engineering and Technology Center. The company plans to scale the solution independently across plants in Taishet, Boguchany, and Sayanogorsk within the next few years.
Following a successful pilot at the Taishet Aluminum Smelter (TaAZ), the system is poised to become a cornerstone of RUSAL’s digital strategy. Beyond production gains, the project is set to drive demand for high-skilled professionals—data engineers, AI developers, and systems integrators—across the Krasnoyarsk Territory, Irkutsk Region, and Khakassia.
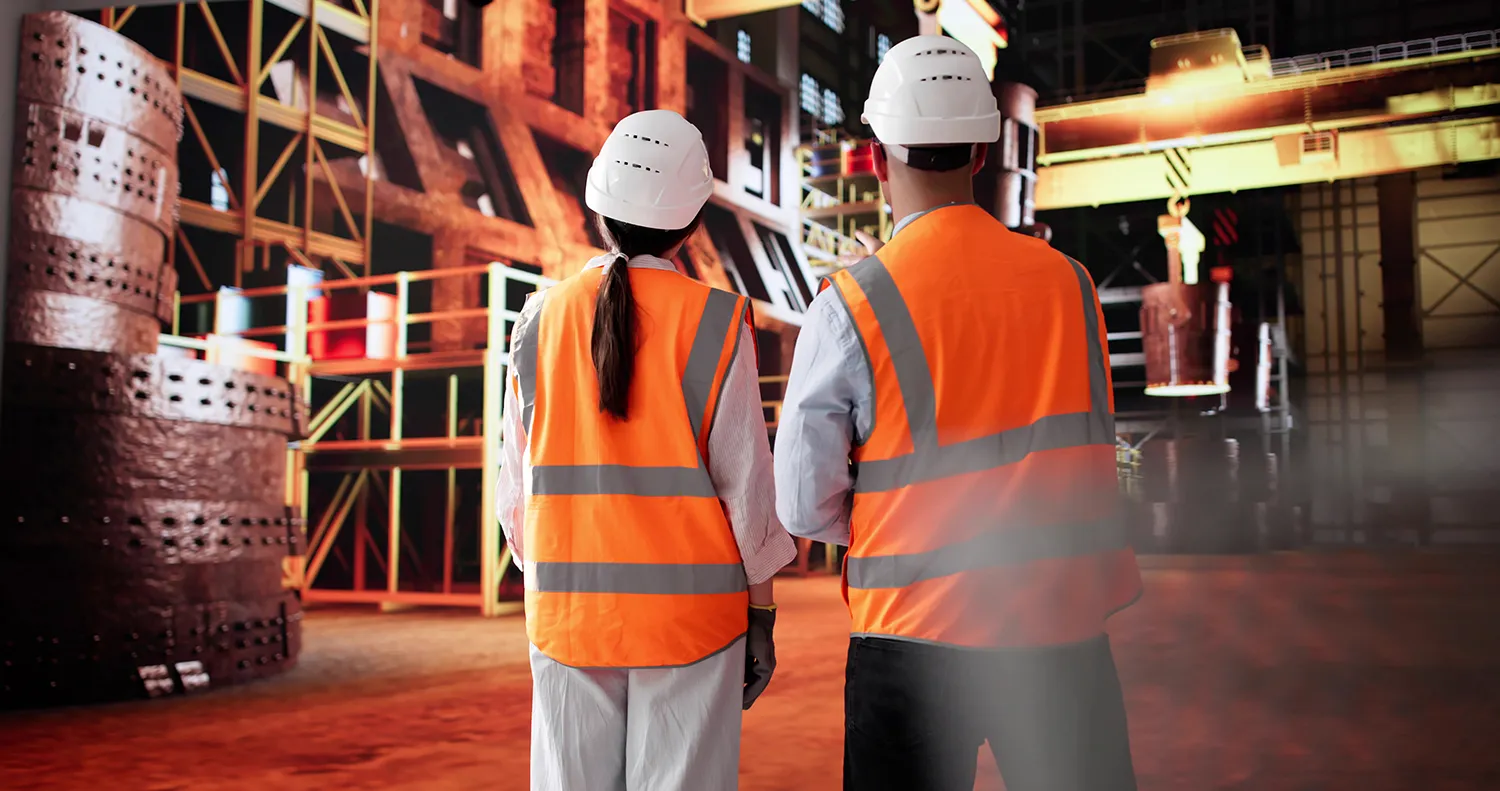
Industrial AI 4.0 with Global Ambitions
RUSAL’s system is not confined to internal use. It has strong export potential, especially for international operations under the company’s umbrella. With the global aluminum sector seeking digital transformation and productivity gains, RUSAL’s model could set a new industry standard.
The technology’s core principles are adaptable beyond metallurgy—to petrochemicals, machinery manufacturing, and chemical processing—any field requiring high-precision, visual control of complex industrial processes. The RUSAL case is not an anomaly but part of a national trend: Russia’s industrial digitalization, backed by state programs, is accelerating toward maturity.