Digital Technologies Drive Efficiency Gains at Russian Industrial Enterprises
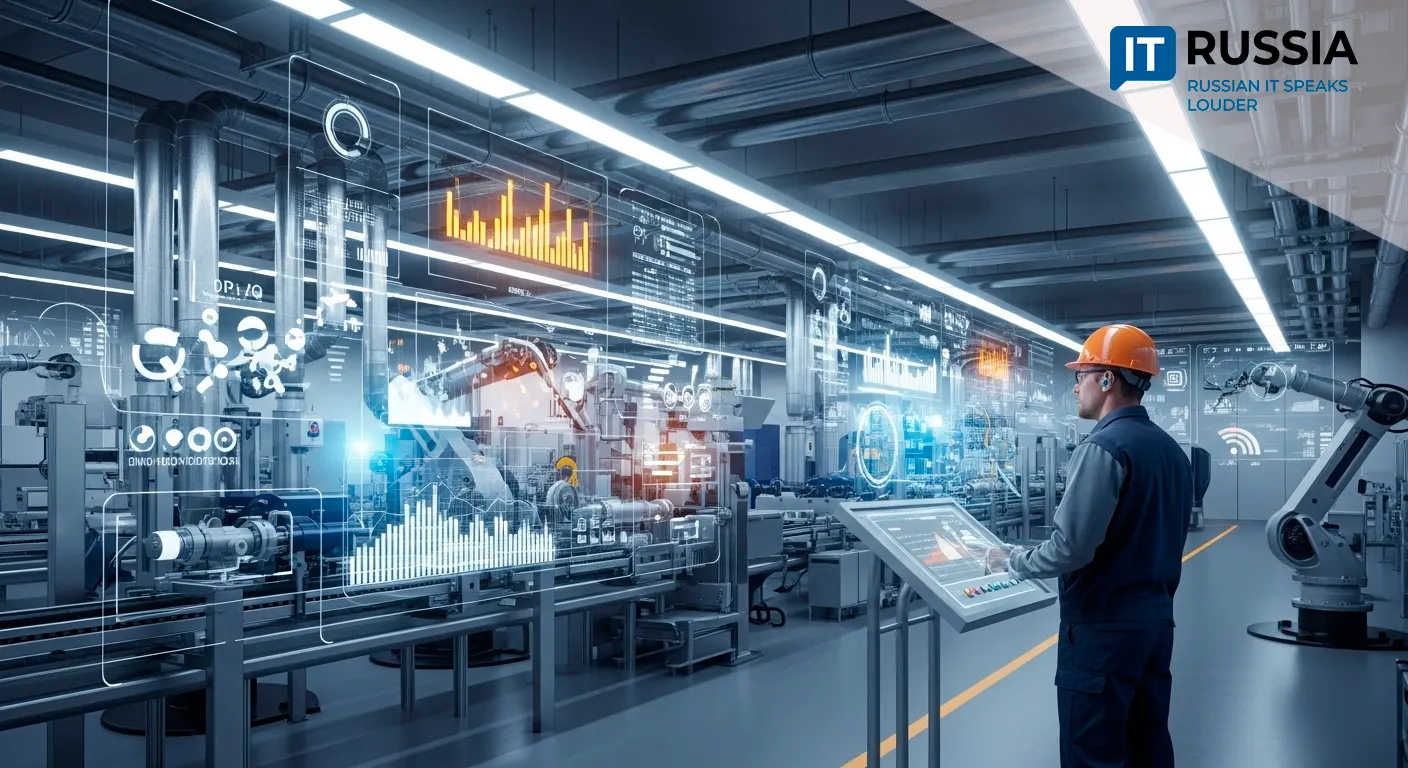
Digital transformation is becoming a cornerstone of Russia’s industrial strategy, boosting productivity and reducing downtime across sectors from metallurgy to energy.
Industrial Modernization Through Digital Monitoring
Artificial intelligence, the Internet of Things (IoT), and remote monitoring technologies are rapidly becoming standard across Russian industry. One standout example comes from the Sinarsky Pipe Plant (SinTZ), part of the Pipe Metallurgical Company (TMK), which implemented a remote monitoring system for its T-4 oil pipe production line.
By establishing a hardware network through its Production Automation Center, SinTZ engineers can now perform diagnostics and system analyses from the lab—eliminating the need to be physically present on the production floor. The monitoring system records and archives real-time data on equipment operation, enabling rapid failure diagnosis and direct communication with specialized technicians such as electromechanics or equipment repair engineers.
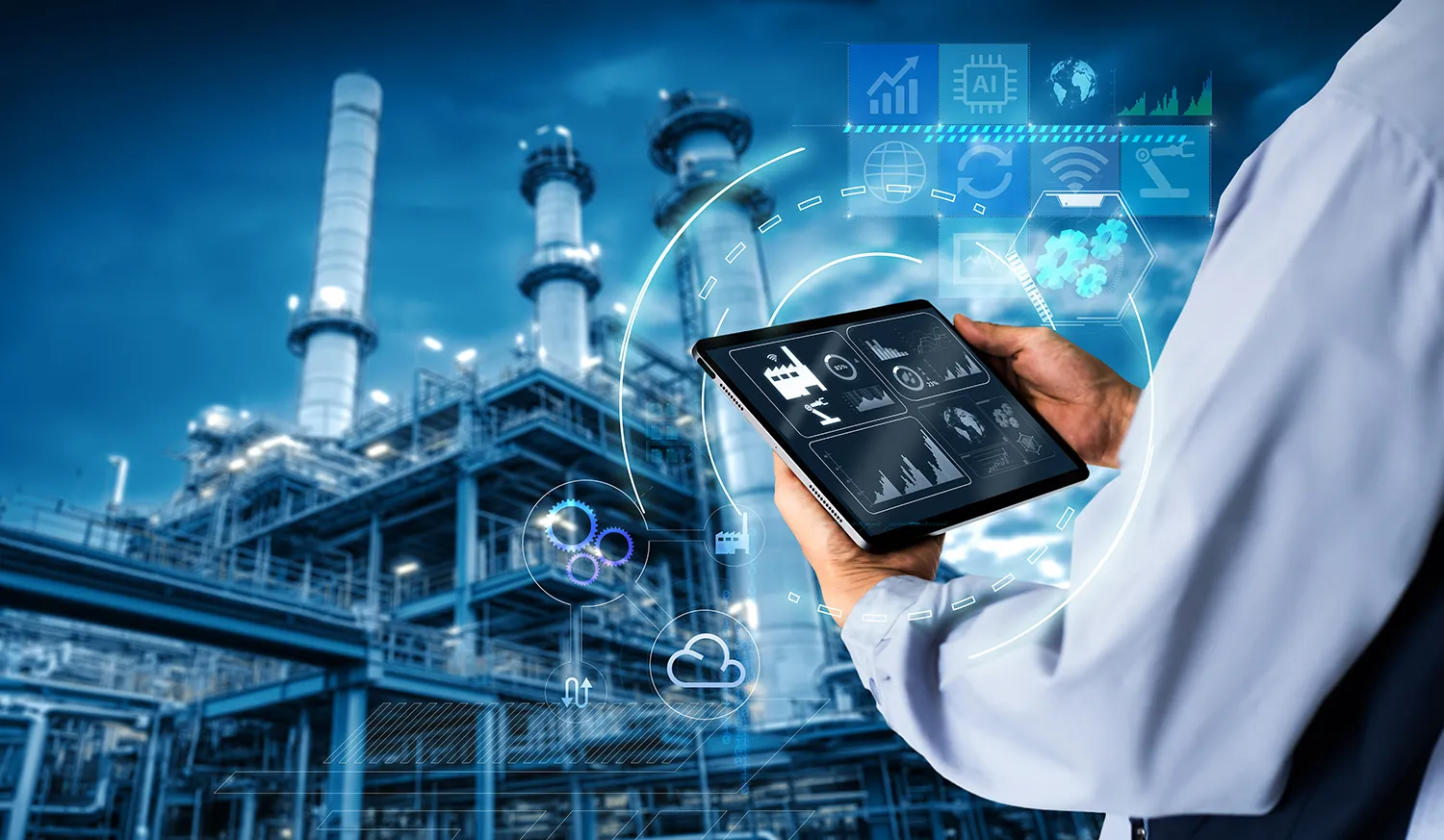
The implementation of this system has reduced downtime by 20%, directly cutting production losses, enhancing reliability, lowering maintenance costs, and improving in-shop logistics and repair workflows. TMK’s initiative offers a tangible example of how Russian digital solutions can deliver operational impact and serve as a benchmark for other domestic manufacturers.
Aligned with Global Industry 4.0 Trends
While the SinTZ case has localized origins, it aligns with global Industry 4.0 trends. Though its global influence is still developing, the approach is universal and adaptable across countries and industries—particularly oil and gas. TMK’s remote monitoring system could evolve into an export-ready solution for energy and machinery companies abroad, particularly those exploring digital twins and IoT technologies.
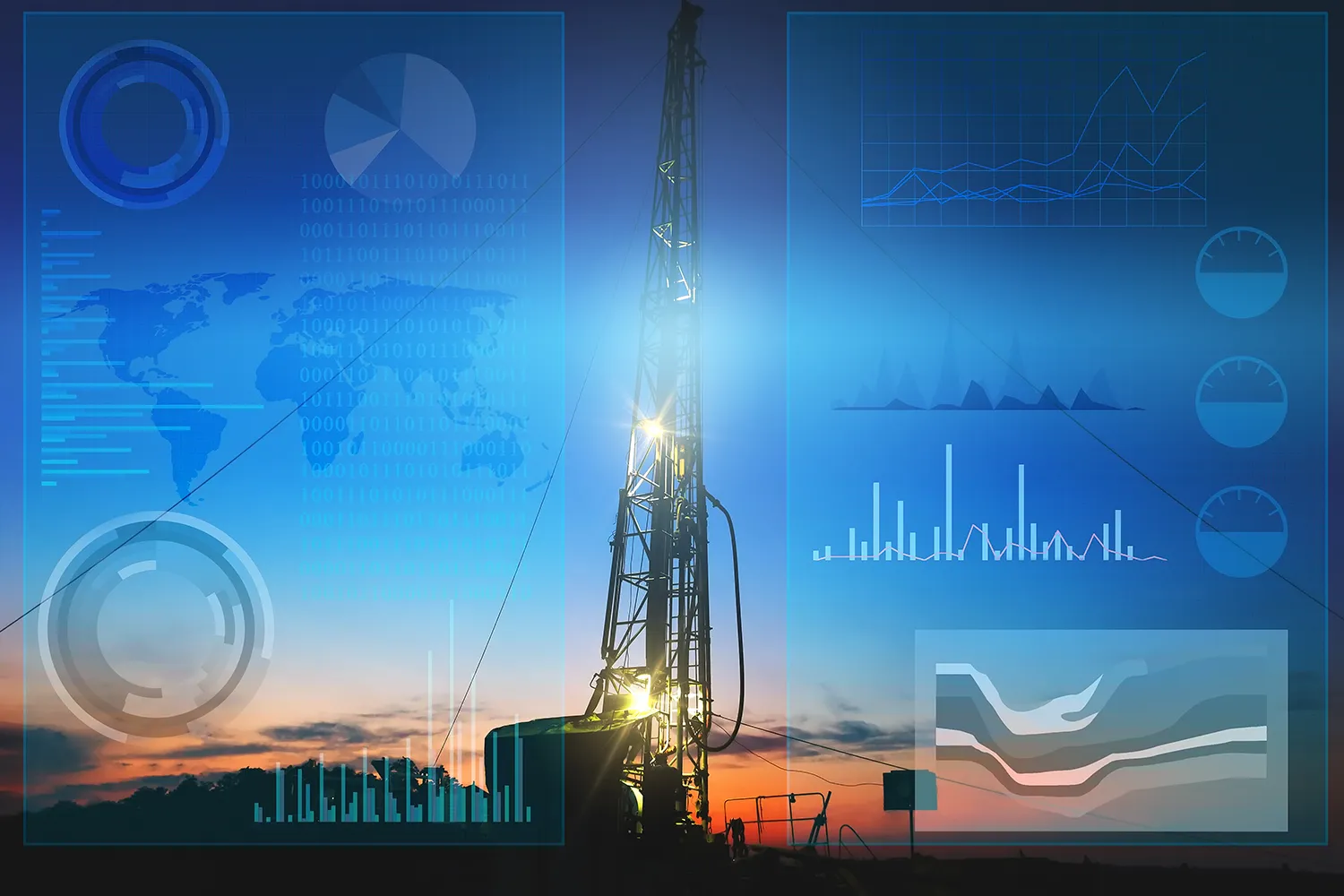
National Adoption of Smart Technologies
Similar initiatives are gaining traction across Russia. Gazprom Neft has launched its 'Digital Cluster' project for remote well monitoring, allowing operators to regulate equipment and ensure safety through integrated smart systems. In 2020, NLMK Group rolled out predictive maintenance for rolling mills using machine vision to detect conveyor misalignment, reducing downtime by 15%. These vision-based systems are now deployed across dozens of use cases—from monitoring moving equipment and technological parameters to emissions control.
Rosatom has enhanced nuclear safety by integrating digital twins for remote reactor monitoring. Meanwhile, SIBUR became the first Russian petrochemical company to switch entirely to a domestically developed Automated Process Control System (APCS). In 2020, it created a proprietary Industrial IoT platform to control IoT devices, collect sensor data, and process operational information.
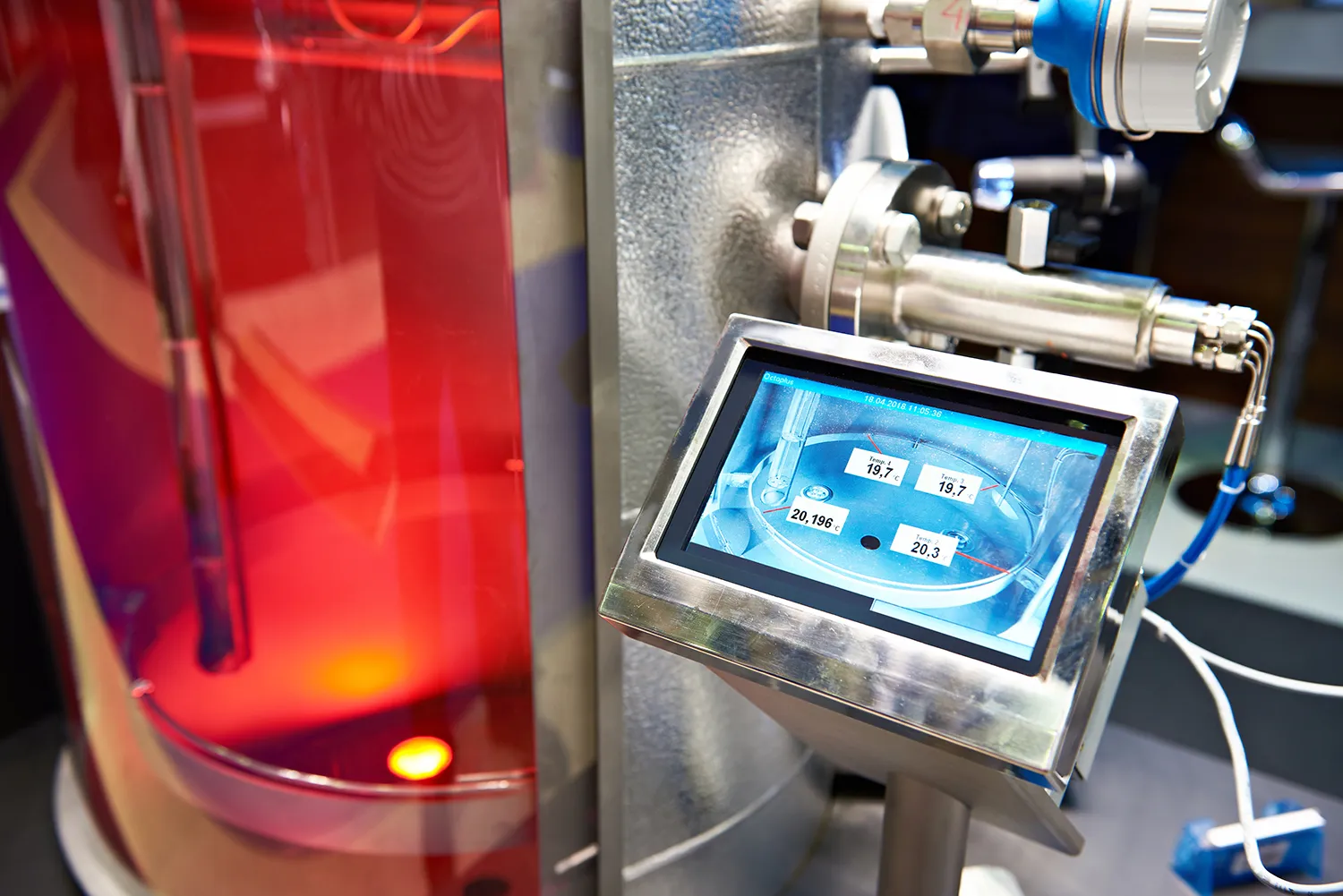
Each of these efforts demonstrates how digital technologies are reshaping productivity and resilience. They not only move Russia closer to sustainable industrial production but also lay the foundation for future investment and wider adoption of digital tools across manufacturing sectors.
Building a National Standard for Industrial IT
SinTZ’s scalable approach can be applied across metallurgy, energy, and agri-industrial enterprises. This aligns with national goals set by Russia’s 'Digital Economy' initiative and 'Digital Production' strategy. The use of IoT devices, edge analytics, and machine learning for failure prediction reflects how modern technologies are becoming ingrained in the country’s industrial practices.